Home ► Bright steel
Machining steel wires
Engineering steels
Tempering steel
Quenched and tempered steels
General construction steels 1.0122 - S235JRC; 1.0579 - S355J2C
Alloyed and unalloyed tool steels
Screwdriver and bit steels
Steels after special analyses for the automotive and aviation industries, etc.
Stainless (material 1.4305), acid and heat-resistant steels
No. | D / EU | USA |
---|---|---|
1.0715 | 11SMN30 | 1215 (ASTM) |
1.0718 | 11SMNPB30 | 12L14 (ASTM) |
1.0719 | 11SMNPB30TE | 12L14 (ASTM) with Te |
1.0720 | 11SMNPBTEBI | 12L14 (ASTM) with Te & Bi |
1.0737 | 11SMNPb37 | 12L14 (ASTM) with S > 0,34% |
1.7139 | 16MNCRS5 | ASTM A108 |
1.7142 | 16MNCRPBS | ASTM A108 with Pb< 0,35% |
1.0401 | C15 | 1015 AISI |
1.0403 | C15Pb | 1015 AISI with Pb < 0,35% |
1.0501 | C35 | 1035 AISI |
1.0502 | C35Pb | 1035 AISI with Pb < 0,35% |
1.0503 | C45 | 1043 AISI |
1.0504 | C45PB | 1043 AISI with Pb < 0,35% |
No. | D / EU | USA |
---|---|---|
1.5511 | 3582 | 3582 |
1.5513 | 4582 | 4582 |
1.0726 | 35S20 | 1140 AISI |
1.0756 | 35SPb20 | 1140 AISI with Pb < 0.35% |
1.0727 | 46S20 | 1146 AISI |
1.0757 | 46SPb20 | 1146 AISI with Pb < 0.35% |
1.0762 | 44SMN28 | 1144 AISI |
1.0763 | 44SMnPb28 | 1144 AISI with Pb < 0.35% |
1.4104 | X14CrMoS17 | 430 F (AISI) |
1.4301 | X5CrNiMo18-10 | 304 N (AISI) |
1.4305 | X8CrNiS18-9 | 303 AISI |
1.4401 | X5CrNiMo17-12-2 | 316 AISI |
1.4571 | X6CrNiMoTi17-12-2 | A182 (ASTM) |
Other material qualities on request |
Styles | Forms of delivery
Rod lengths 1,500 - 6,300 and/or 7,000 mm (-0/+50 mm)
Narrower tolerances are available on request.
Bars are crack-tested from 6 mm upwards, round and hexagonal, bevelling, surface milling and planning on request.
Coil weights | 1,000 - 3,000 kg | ~ 2.205 - 6,614 lbs |
Rings | 250 - 2,000 kg | ~550 - 4,410 lbs |
Coils | 500– 2,000 kg | ~1.102 - 4,410 lbs |
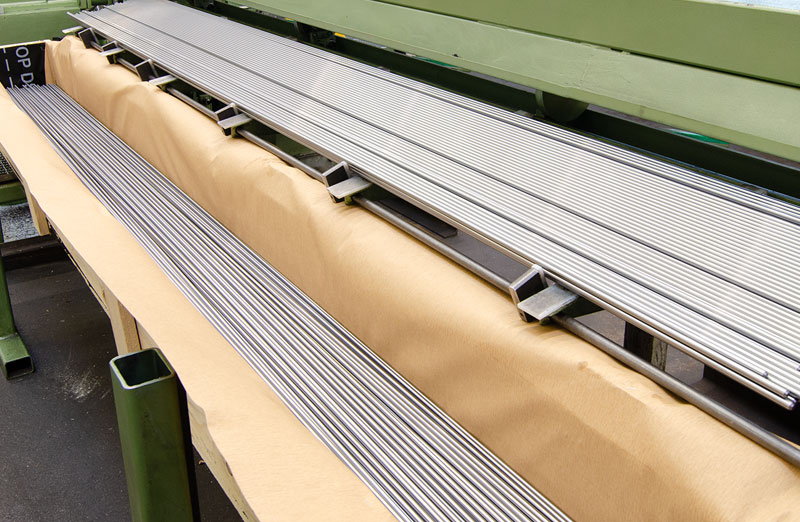
Grinding process
Ground round steel is produced by machining drawn bars. This process allows round steel to be produced with maximum precision in terms of tolerance (up to ISO 6, e.g. h6), roundness and a controlled, homogeneous surface roughness.
The result is an elegant surface with a satin finish.
Another special feature is that a technically crack-free and/or decarburisation-free surface can be achieved through the targeted use of the grinding process.
Areas of application:
- Automotive industry
- Machine tools
- Precision engineering
- Furniture industry
- Electrical industry
- Manufacture of connecting elements
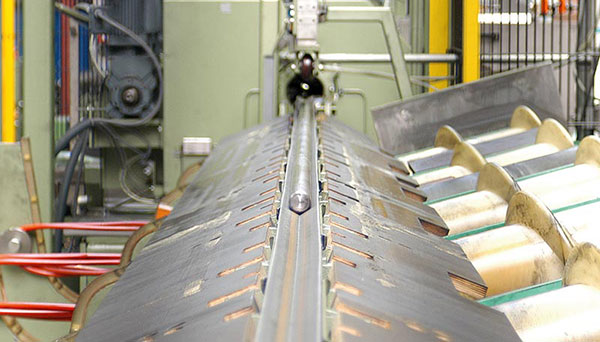
Das Prüfsystem arbeitet statisch ohne Rotation.
Areas of application
Automated ultrasound testing is used for the non-destructive 100% inspection of internal material defects, as well as for measuring and testing the layer thicknesses of function and safety-critical components.
User industries include the automotive supplier and automotive industry, foundries and manufacturers of containers and semi-finished products.
Test procedure
Ultrasound testing is used to detect edge defects (longitudinal defects) and core defects in the entire cross section. The coupling of the ultrasound signals takes place using a submersion system,
i.e. during the test, both the test heads as well as the specimens are under water.
Edge defect testing of the round material
The test heads, which are arranged on several levels, are rotated against each other via a central adjustment unit so that the test heads on one level sound exactly into the holes of the next level. This ensures that the test heads do not test redundantly and the edge area is covered 100%.
Edge defect testing of a hexagonal rod
The intromission angle is set centrally to a set
angle for all test heads on a test pad.
Core defect testing on round material
The intromission angle of the test heads is positioned vertically. This ensures that the test heads do not test redundantly, the edge area is covered
100% and the direction-dependent defects are picked up.
Core defect testing of a hexagonal rod
The intromission angle of the test heads is
positioned vertically. The dimension-dependent activation of the test heads and the selection of two aligned positions ensure that the test heads do not test redundantly and that the core area is
covered 100%.
How can we help you?
We will of course be happy to assist you personally.
You can reach us weekdays between 8:00 am and 5:00 pm.
Stefan Schneider | Head of ProfitCentre0049 2381 276 264 |
Jochen Specht | Sales |0049 2381 276 247 |
Heike Strahberger | Sales |0049 2381 276 246 |
Kai Dicken | Sales |0049 2381 276 239 |
Andrees Kuhlmann | QMM & techn. Kundensupport |+49 2381 276 469 |
Tina Zöllner | Sales |0049 2381 276 267 |
Zoran Kos | Sales |0049 2381 276 245 |
Hendrik Schwarte | Sales |0049 2381 276 340 |
Stefan Schneider | Head of ProfitCentre0049 2381 276 264 |
Julia Rohrbacher | Sales |0049 6332 800 416 |
Katja Jochem | Sales |0049 6332 800 412 |
Heike Simon | Sales |0049 6332 800 415 |
Andrees Kuhlmann | QMM & techn. Kundensupport |+49 2381 276 469 |
Alexandra Germann | Sales |0049 6332 800 424 |
Michaela Westrich | Sales |0049 6332 800 440 |
Lars Beckmann | Head of ProfitCentre0049 2304 94 112 12 |
Ezzedine Barnaoui | Sales |0049 2304 94 112 16 |
Marcel Bock | Sales |0049 2304 94 112 22 |
Moritz Nisipeanu | Sales |0049 2304 94 112 28 |
Daniel Badura | Sales |0049 2304 94 112 14 |
Sabrina Lammertz | Export sales |0049 163 27 69 500 |
Andrees Kuhlmann | QMM & techn. Kundensupport |+49 2381 276 469 |